Con un gallo incorporado en el parabrisas delantero, la nueva Mégane E-TECH Eléctrica muestra con orgullo sus orígenes franceses, fabricada en la fábrica de Douai (norte de Francia) en el centro ElectriCity. La cadena de montaje de la histórica fábrica de Renault tuvo que ser completamente revisada para poder acoger la producción de autos totalmente eléctricos. Un reto industrial que Nicolas y Vincent, responsables del proyecto de montaje, ayudaron a superar con éxito. Más información sobre las personas y las máquinas que están detrás de esta historia. Con la nueva Alliance Standard Line, el futuro de la fabricación de Douai será eléctrico.
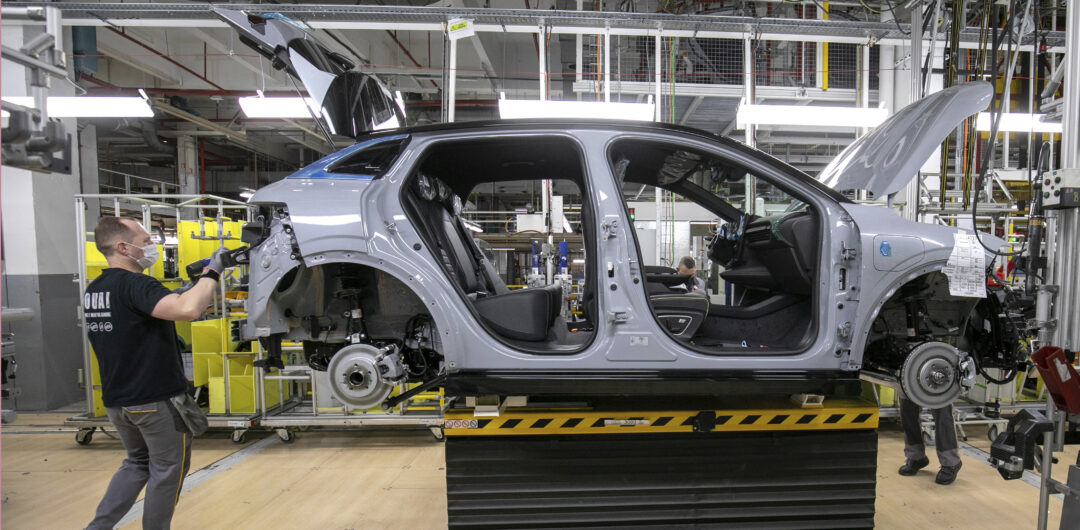
Siete semanas de obras, 38,000 m2 de espacio vacío, 100 unidades de maquinaria pesada (robots y equipos de asistencia) y 400 puestos de trabajo redistribuidos. Estas cifras dan una idea de la magnitud del reto que supone la instalación de la nueva línea de montaje «Alliance Standard Line» en la fábrica de Douai. Una transformación necesaria para que la histórica fábrica de Renault -que en su momento fabricó el Renault 5, el Renault 14, el Renault 19, el Renault 21, el Mégane y el Scenic- acoja ahora la producción de la nueva Mégane E-TECH Electric. Nicolas y Vincent, directores del proyecto de montaje, reflexionan sobre su gran aventura.
«Estamos muy orgullosos de haber participado en esta aventura, porque un proyecto de tal magnitud, nada menos que en Francia, ¡es una oportunidad única en la vida!» comentaron Nicolas (Jefe de Proyecto de Montaje de Capacidades) y Vincent (Jefe de Proyecto de Montaje de la nueva Mégane E-TECH Eléctrica).
La cadena de montaje de la fábrica de Douai: donde se unen rendimiento y versatilidad
«En una fábrica, más que en cualquier otro lugar, el tiempo es preciado. No podíamos tolerar ni un solo retraso», dice Nicolas. La pauta está marcada. Había que evitar a toda costa cualquier día de inactividad. «Una excepción: las reparaciones y mejoras necesarias se hacen el fin de semana, o por la noche… o en agosto, durante las vacaciones de verano. Si cada sección de la antigua línea de montaje se pusiera de punta a punta, la línea de montaje, con los 400 puestos de trabajo, tendría casi 1,700 metros de longitud. El tamaño gigantesco de la línea se explica por su antigüedad: la última vez que se modernizó por completo fue en 1986», afirmó Nicolas.
La fábrica de Douai produce Renault desde 1975. Con más de 10 millones de vehículos emblemáticos que han salido de las puertas de la fábrica. «No es que la división de ensamblaje de Douai fuera vieja y anticuada. Antes de las recientes obras, la capacidad de producción de la fábrica era muy buena. Había que sustituir la línea para poder producir tanto vehículos con motor de combustión interna como con motor eléctrico. Matamos dos pájaros de un tiro al poner toda la línea al más alto nivel de las normas europeas», explica Vincent.
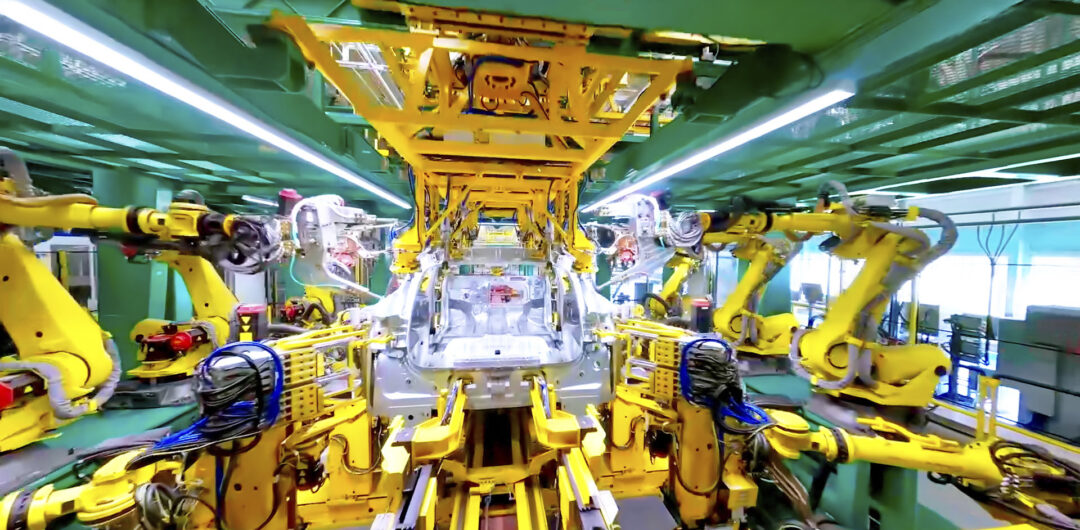
Sobre el papel, el objetivo es claro: crear una nueva línea de montaje con la tecnología más avanzada de la Alianza Renault-Nissan-Mitsubishi, manteniendo todo lo que se pueda conservar. En concreto, eso significaba vaciar por completo el edificio de ensamblaje con una superficie de 38,000 m2, eliminando la primera planta, al tiempo que se sustituyen más de 100 piezas de maquinaria pesada (robots y equipos de asistencia) y 400 puestos de trabajo junto con todo el equipamiento necesario.
«Tardamos un año en preparar el lugar de trabajo. Tras un minucioso análisis, determinamos que se podía mantener el 20% de la antigua línea de producción», recuerda Nicolas.
Las líneas de chapa y ensamblaje de la fábrica de Douai son ahora compatibles con la «Alliance Standard Line«, el estándar de producción más avanzado dentro de la Alianza Renault-Nissan-Mitsubishi. La planta, muy versátil, puede ahora producir tanto vehículos con motor de combustión interna como con motor eléctrico en la misma línea, con tres plataformas diferentes y con los mejores estándares de seguridad y rendimiento posibles.
Un diseño vanguardista para mejorar la ergonomía y la seguridad del puesto de trabajo
Contrariamente a lo que podría pensarse, la capacidad de producción de la fábrica de Douai no ha sido el motivo de la reciente actualización. La producción de 60 vehículos por hora, previa a las obras, sigue siendo la misma. La razón principal de la modernización del complejo industrial era mejorar la eficiencia del proceso de producción para mejorar la ergonomía de los puestos de trabajo y la seguridad de los operarios.
«El mejor ejemplo es cómo las alturas de las carrocerías varían según el tipo de vehículo. En los tramos en los que se montan los paneles interiores y exteriores (CT1-CT2), el vehículo se coloca sobre unas planchas que actúan como base. Se puede subir o bajar entre 20 cm y 1.3 m de altura para facilitar el trabajo de los operarios. Se ha hecho mucho para mejorar las condiciones de los que trabajan en los bajos», explica Vincent.
Esta enorme actualización fue una oportunidad única para que los expertos en ergonomía de Renault Group mejoraran a fondo y optimizaran los puestos de trabajo para que las tareas se llevaran a cabo de forma más fácil y fluida. «Los autos de herramientas se han integrado en la línea y siguen como las piezas que ahora entregan los robots conocidos como «AGV» (Auto Guided Vehicle). Los operarios no tienen que desplazarse tanto ya que tienen todo al alcance de la mano. Menos desplazamientos y menos manipulación significan menos fatiga y más productividad. Sin el riesgo de que las piezas se equivoquen o se dañen. La calidad mejora», afirma Nicolas.
La guinda del pastel es que la reciente actualización también ha supuesto un ahorro de energía con la instalación de luces LED.
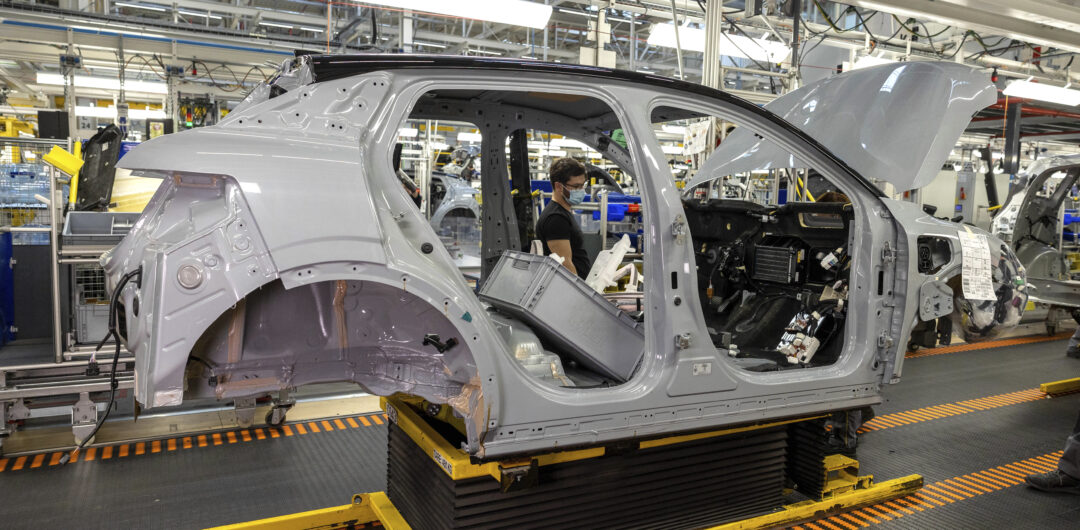
Siete semanas de inactividad
Las obras del proyecto duraron algo menos de dos meses, desde el 25 de noviembre de 2020 hasta el 18 de enero de 2021, cuando se reanudó la producción. Un total de 1,200 personas trabajaron incansablemente en la actualización, incluso hasta la temporada de fiestas.
«Mantuvimos a todo el mundo motivado asegurándonos de que el ambiente fuera agradable. En Nochebuena, montamos un árbol de Navidad de 3 metros de altura con las imprescindibles luces navideñas dentro del edificio. ¡Qué recuerdo tan especial! «, comentan Nicolas y Vincent con una sonrisa.
La impecable movilización y organización dio sus frutos: las obras propiamente dichas para la modernización sólo duraron siete semanas. Qué mejor recompensa para el concienzudo esfuerzo realizado por todos los que participaron en una aventura técnicamente tan desafiante que unió a las personas.
La nueva línea de montaje es más compacta que la anterior. Los 20,000 m2 de superficie liberada por las obras se han reutilizado para instalar un taller de montaje de baterías.
La logística externa e interna de las instalaciones se ha rediseñado por completo. El depósito de camiones y el departamento de logística de piezas están ahora junto a la línea de montaje. El uso de kits completos para cada vehículo hace que ahora sea más rápido y eficaz hacer llegar a los operarios las piezas que necesitan.
La emoción y los nervios estaban a flor de piel el 18 de enero, cuando se reabrió la línea de montaje por primera vez desde que comenzó la modernización. «Celebramos el éxito de la reapertura cenando todos juntos en las instalaciones. Pedimos 200 pizzas. Sabían la victoria». recuerdan con cariño Nicolas y Vincent.
La línea sigue en fase de rodaje. Recientemente ha alcanzado el umbral de 60 vehículos/hora. Desde su reapertura, han salido de la línea 3,000 Megane E-TECH Electric, reconocidos por la calidad de su fabricación. «La nueva Mégane E-TECH Eléctrica ha sido coronada con una calificación de 5 estrellas Euro-NCAP. Un reconocimiento a la calidad de diseño y fabricación del auto. Un vehículo excepcional nacido en condiciones ideales. La calidad está ahí. Esa es nuestra mayor recompensa», afirma Vincent con orgullo.
Un futuro electrizante para la fábrica de Douai
Desde la modernización, la fábrica ha ido cogiendo ritmo poco a poco. Acaba de alcanzar su nivel de producción «normal» de 60 vehículos/hora. Este tipo de producción significa que la fábrica de Douai, que celebró su 50º aniversario en 2020, tiene un futuro brillante por delante, en el corazón de ElectriCity.




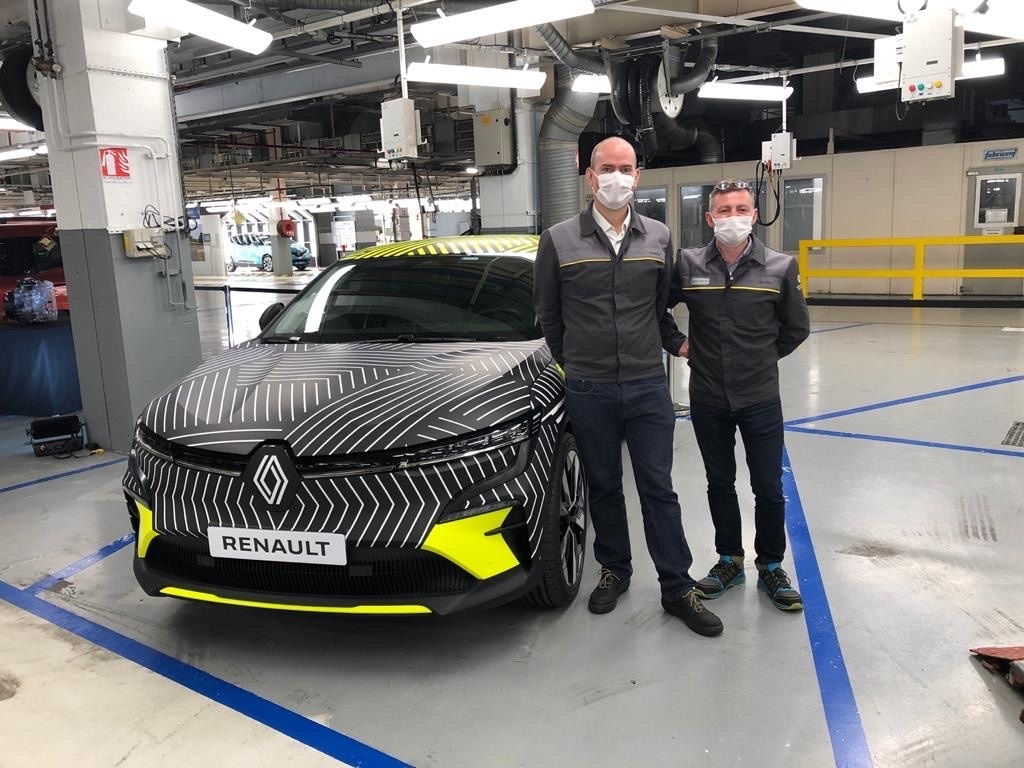